Electrical Energy Savings through Efficient Energy Management
Research Question: Despite the difficulties of getting time to address the energy management topic, it is crucial for companies and organizations to know at least the basics of the topic and much they can save if they invest in considering it. So through this paper, the research questions are: Why energy management and the global need to save energy is important, what are the opportunities to save energy, and what are the barriers and policies?
Energy Management
Energy management is all about reducing the cost of energy used by an organization, now with the added spin of minimizing carbon emissions as well (Anastasi et al., 2011). Reducing energy costs has two facets: price and quantity. Power efficiency is the utilization of less power for a similar or maximized output. It is rapidly being defined as a cost effective and important remedy for minimizing greenhouse gas emissions generated as part of the company activities, including the steel and iron industry. As a fact, power efficiency has the technical ability to decrease the company's power use by 20% (Berthouex, 2019) . The significance of the ability is clearly made when considering the current companies which are responsible for about 26% of CO2 emissions (Berthouex, 2019).
Significantly, power efficiency not only minimizes GHG emissions but also boosts an industry's productivity and competitiveness. Operational stable power-efficient projects may also cause spillovers bringing about an industry-wide better efficiency, which results to raised company value. With regards to the steel and iron sector an estimate by the International Energy AgencyIEA demonstrates that the technical potential exists to minimize power usage by 20% (Vesma, 2009). The estimate includes the accountable improvements that have been established over the years in the industry.
The phases of the formation of energy policy, energy planning, auditing, and implementation and operation are followed by a state of constant checking. This is in turn supported by an internal auditing system, processes for monitoring, measurement, and analysis as well as for nonconformities, correction, corrective and preventive action. A periodical management review completes the cycle.
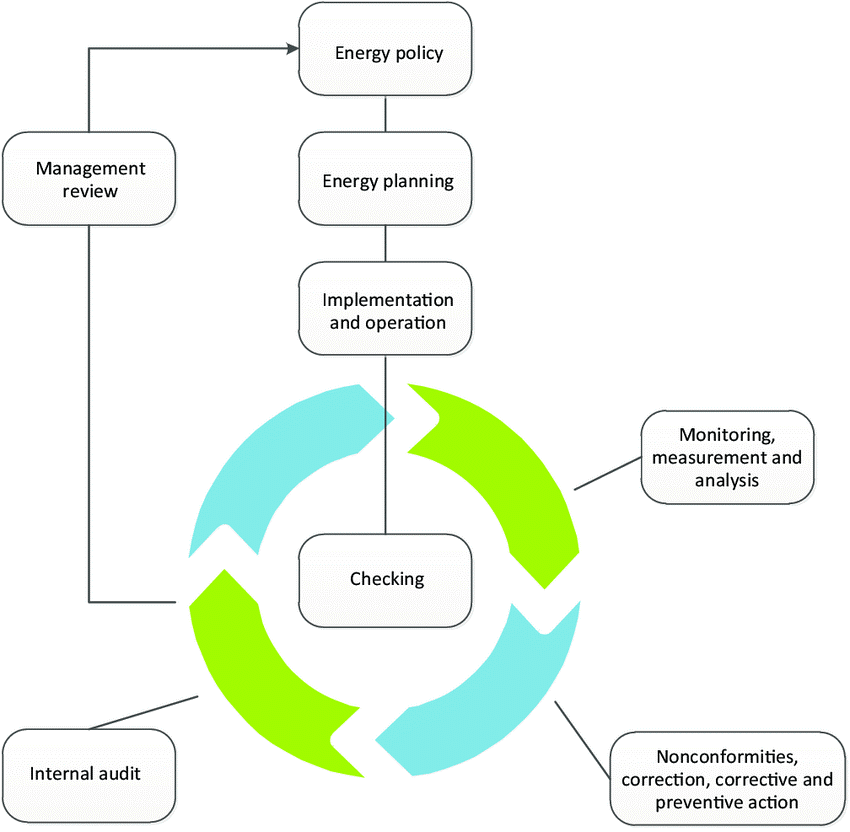
Energy management system methodology (Berthouex, 2019).
The steel and iron company are the second biggest power consumer in the industrial environment, with power expenses of about 20-25% of the total expenditure for steel and iron providers. Decreasing these expenses has therefore been the most significant steel production priority (NOJAVAN, 2020). Sometimes, however, companies view power savings as either benefit as a result of emerging investments, rather than a major component approach to enhance value generation. Further, real power-efficient raises are usually termed as the only implementable through normal high expense technological investments (Department of Energy: Republic of South Africa, 2005).
The following pie chart depicts the estimated costs of owning and operating an oil-fired furnace to heat a 2,000-square foot house in the northeast United States. Of note is that the initial costs represent only 23% of the total costs incurred over the life of the furnace.
The life cycle cost approach provides a significantly better evaluation of the long-term implications of an investment than methods, which focus on first cost or near-term results.
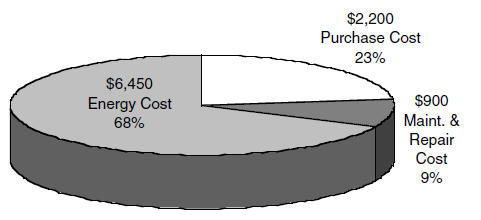
15-Year life cycle costs of a heating system(Petrecca, 2014).
Industrial power efficiency is usually accomplished as much through changing the operational mechanisms of an industrial site which installation of the Best Available Technologies (BATs) (Energy Institute, 2016). As standalone BAT investments are significant in full energy achievement, implementation of a power management system is too important to prioritize and identify the entire power-efficient practices in advance of important investment plans in relation to the physical investment. Industrial experience has demonstrated that industries can save around 10-30% in a year of their power consumption (Petrecca, 2014). This means the operating costs are reduced through power management methods, much of the changes including operational utterances. Application of the best practices can promote power saving opportunities with minor paybacks of not more than two years (Mohamed & Khan, 2017).
The implementation of an EnMS to boost power performance, industries optimize their systems and boost overall system monitoring efficiencies (S Shashi, 2004). Subsequent benefits for production for industries utilizing an EnMS also involve capacity utilization and enhancing productivity, pollution and reduced use of resources, and lower maintenance and operational costs which contribute to an increase the value promoting company competitiveness (Mohamed & Khan, 2017).
Energy Management Value
Industries, businesses, and governmental sites have all undergone unbelievable environmental and economic pressures recently (NOJAVAN, 2020). Economic competitiveness in the world marketplace and achievement of rising environmental standards in order to minimize water and air pollution has grown to be the main driving forces in the previous capital cost and operational cost investment opinions in nearly all organizations(Mohamed & Khan, 2017). Power management has therefore served as a significant tool in promotion organizations to accomplish their critical objectives for a shorter survival period for a long success period (Nulty, 2014).
The challenges faced by companies both nationally and individually include:
Achieving the most striking environmental quality standards, majorly in relation to global warming reduction and acid rain prevention. Power management promotes better environmental quality. As the major global warming culprit is carbon dioxide. A chemistry equation involving the burning of methane demonstrates that 2.75 pounds of CO2 is generated when a pound of methane is burned. Therefore, power management, by reduction of methane burning can significantly minimize the CO2 amount in the environment hence global warming reduction. Industrial and commercial power use implies 45% of the CO2 generated from the combustion of fossil energy and around 70% of the SO2 emitted from stationary resources (Nulty, 2014). Power management minimizes a load of energy plants, as fewer electricity Watts are required. When a plant burns fuel oil or coal, an amount of acid rain is generated from the emitted Sulphur dioxide by the plant.
Through power management then the acid rain is reduced. Minimal power consumption enhances minimized thermal pollution at plants and minimal water-cooling discharge. Minimized cooling necessities and efficient requirement satisfaction promote lower Chlorofluorocarbon CFC usage and minimize ozone layer depletion around the stratosphere (Shimy, 2018). Therefore, power management promotes improved environmental standards.
Becoming continually economical competitive in the world marketplace, that needs minimizing the production cost or the quality of the services, decreasing company power inventiveness, and achieving the consumer service requirements for delivery periods and quality. Similar power and expenditure savings are achieved through power management (Vesma, 2009). Power management can bring profit and loss difference and formulate a real competitive industry enhancement. Power management in the approach of new power technology implementation, new resources and new operational processes in addition to new technology in material and equipment for industry and business to boost productivity and improve their product and service quality (Walter Kahlenborn, Sibylle Kabisch, Johanna Klein, Ina Richter, 2015). Often, power savings is not a major factor when industries plan to buy new equipment, apply new processes, and utilize new technological materials.
The need for improved quality increased productivity, decreased power costs, and decreased environmental pollution gives a powerful basis for industries and organizations to adopt the new changes (Vesma, 2009). Total quality management TQM is an extra emphasis that organizations and businesses deployed recently. TQM is considered an integrated mechanism to facility operation and power cost control ought to be improvised in the TQM practices (Anastasi et al., 2011). TQM works under the principle that changing authority is available to the front-line workers while other plans should be at the lower facility operating levels. If workers have power management skills, they can engage in making recommendations based on decisions about power costs (Energy Institute, 2016).
Power Management Systems
A power management system is an operational process for improving power performance and increase power savings continually. An EnMS accomplishes this for industries in the steel and iron environment by the establishment of an industrial facility framework to control their power use and define approaches to implement power-saving technologies, involving those approaches that require no capital investment (Horinov, 2017). The EnMS ensures that power efficiency improvements happen not only once but continuously identifying and implementing a constantly improvement process. Research establishes that even optimal systems lose their original efficiency gain timely because of production and personnel changes if power efficiency is not practiced in other management operations (Petrecca, 2014).
Implementation of the EnMS is dependent on the available ISO 50001 power management standards or a customized EnMS approach (Department of Energy: Republic of South Africa, 2005). The major focus on an EnMS, independent on the taken approach, is that it consists of all functions and levels of the industry and needs a continuous top management commitment. This gives an employee motivation which acts as a major element to an effective EnMS functioning framework. As the case of known management systems, the EnMS is designed into similar managerial structures as strategic objectives and industrial policy.
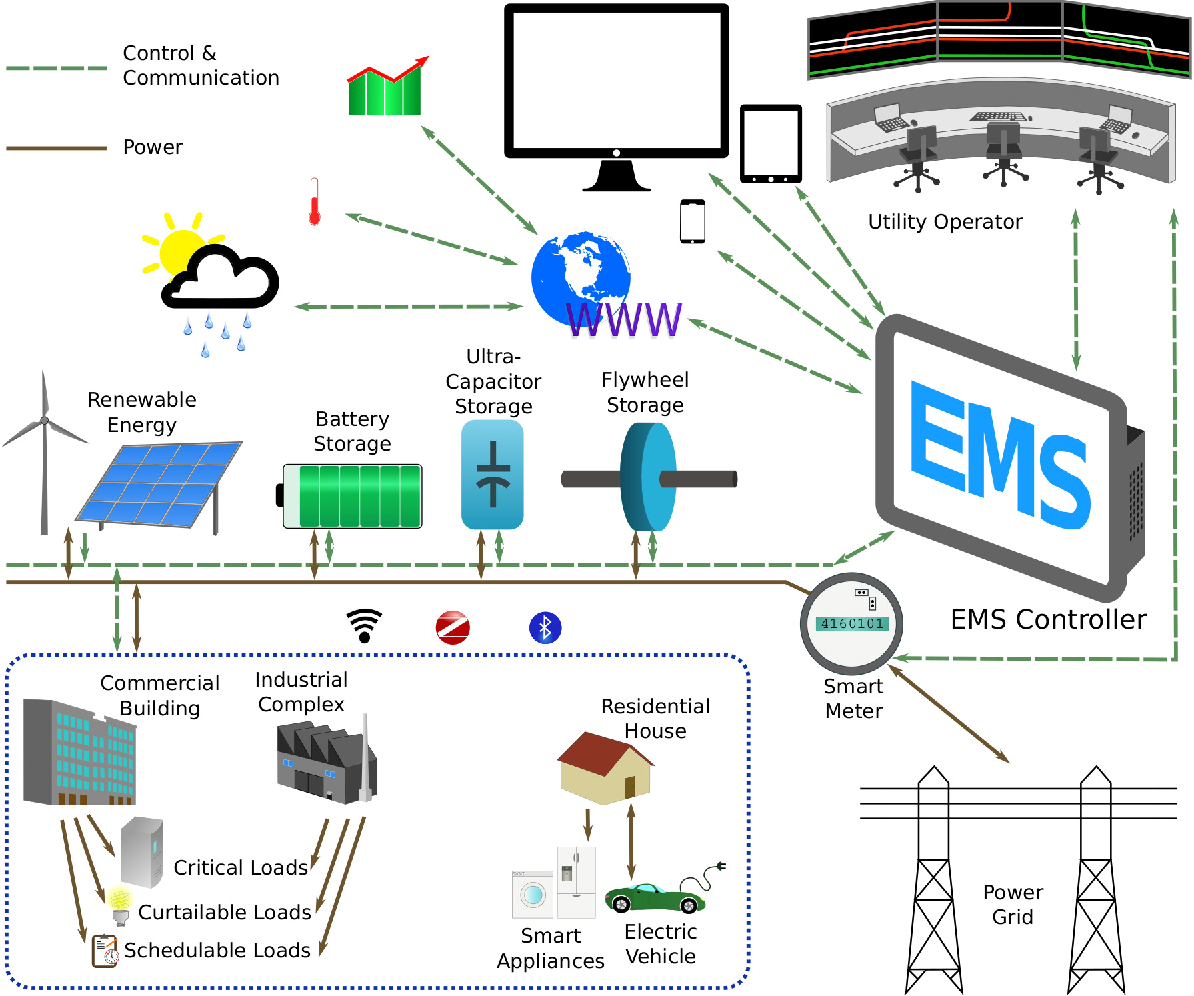
Energy Management System EMS Overview (Berthouex, 2019).
The EnMS besides can operate best in the steel and iron sector when applied in accordance with the recently established ISO 144044 standards, the original document in the sector of the kind that gives a CO2 calculation method for blast furnaces in steel plants (Berthouex, 2019). Combining the power and CO2 monitoring systems establishes the emissions associated with power utilization reduction. This provides the EnMS with extra value as the effect of particular measures can be best assessed and understood (Kanchev et al., 2011). Despite the approach taken whether customized or standardized, the general EnMS process depends on the Plan-Do-Check-Act continuous enhanced framework (Vesma, 2009):
Plan: To perform a power review and define the base, benchmark other same sites, set targets and objectives, establish resources, and generate action plans required to generate results according to the organizational power policy.
Do: To deploy the action layout. Then Check: to control and measure the procedures. Give a target achievement review and effectiveness review of the EnMS against the power policy objective.
Act: To establish the achievements, take measures to continually boost the EnMS and the power performance implementing new objectives.
On the Plan-Do-Check-Act setup, the full EnMS implementation is dependent on the procedures taken to make sure the improvements are continually established.
The ISO 50001- Energy Management Systems Standard
ISO 50001:2011, an international voluntary standard for power management systems was established by the International Organization for Standardization (ISO). The standards were set to provide organizations with the EnMS requirements. It focuses on several regional and national power management standards, regulations, and specifications, involving Denmark, China, Ireland, the European Union, Korea, Japan, and the US (Walter Kahlenborn, Sibylle Kabisch, Johanna Klein, Ina Richter, 2015).
An EnMS is a suite of procedures and practices that ensure systematic tracking, analysis, and planning of energy use through a Plan-Do-Check-Act framework of continual improvement. The diagram below illustrates the framework and lists the key activities associated with operating an EnMS:
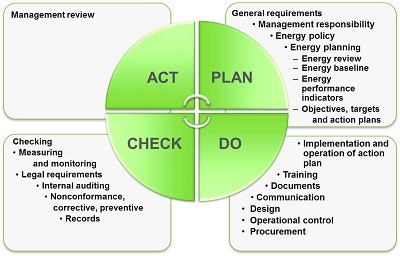
‘’Plan-Do-Check-Act’’ framework of continual improvement (S Shashi, 2004).
The standard is a typical management system standard for processing and services hence can be implemented by distinguished bodies of all basis both private and public sectors. It was developed in a way that could be applied in the presence of other management systems, particularly those under the environmental and quality control or are individually implemented. In the case of ISO 14001, the environmental management, and ISO 9001, the quality management is under the Plan-Do-Check-Act setup (Walter Kahlenborn, Sibylle Kabisch, Johanna Klein, Ina Richter, 2015).
Significantly, the ISO 50001 standards do not allow target fixing for boosting power performance. Instead, it is up to the regulatory authorities or the user organization. This implies that any industry can adopt ISO 50001 according to its own power policy and deploy a continuous power performance advanced process within its budget and capacity resources.
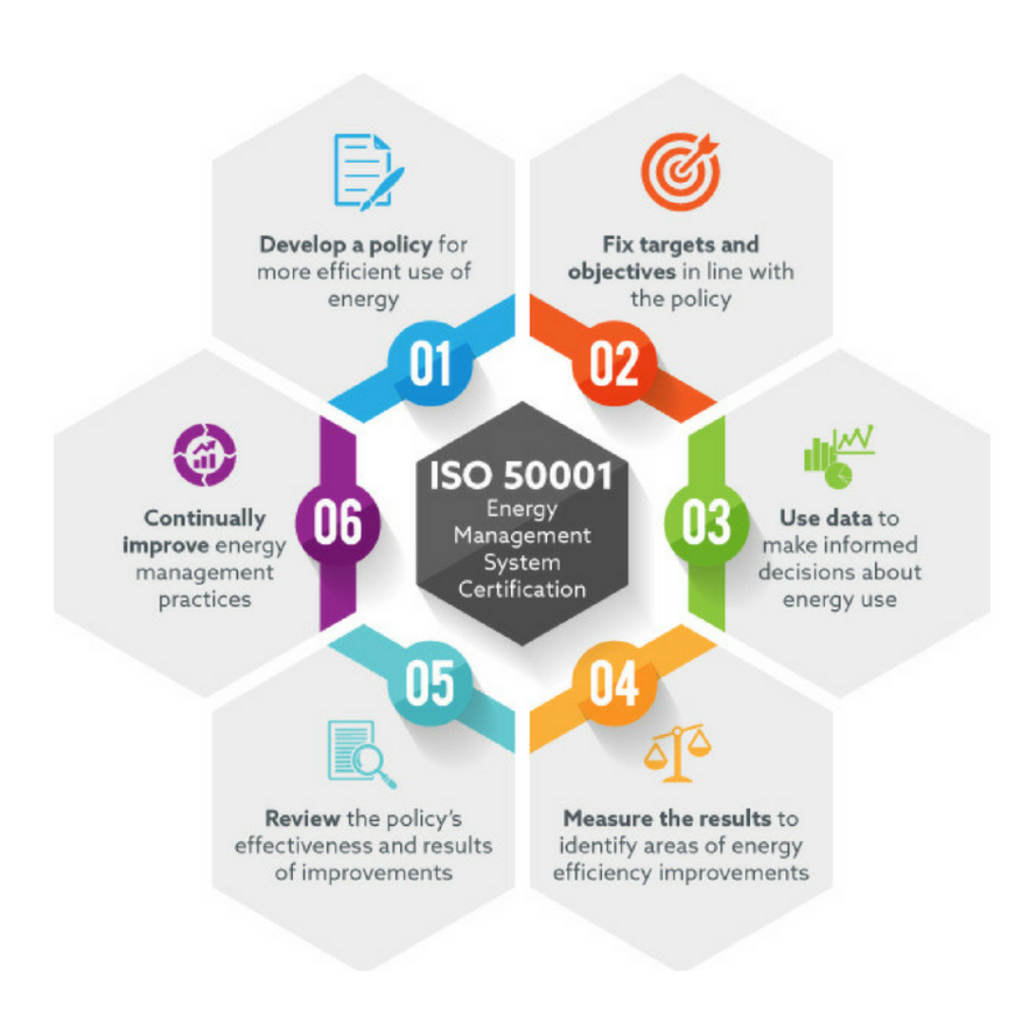
Five Benefits of ISO 50001 – Energy Management System Certification (Shimy, 2018).
Industries that utilize a standardized EnMS as a wider part of the power management system have mostly achieved cost savings more than the achievements of self-designed systems (Shimy, 2018). An example is seen in Ireland whereby industries implementing the standardized EnMS and are involving in the government Large Industry Energy Network (LIEN) system have shown fast power performance advancement, despite power management being an existing technique and achieving important savings in the previous decade even in the absence of the standard EnMS (S Shashi, 2004)......
Are you interested in this article? Write to us for the rest of the research.
Author: Sulaiman Elrajoubi, a student at LIGS University, under the supervision of Dr. Minh Nguyen